HSE Management System (HSEMS)
Our Policy
To ensure the successful implementation of the HSE Policy in its business activities, in FY2007 INPEX developed the HSEMS Manual, referencing standards such as ISO 9001 and ISO 14001. This manual was revised in FY2017 based on the international standard OMS5101, issued by the International Association of Oil & Gas Producers (IOGP). OMS510 is a system whose fundamental principles are leadership, risk management, continuous improvement, and implementation. This system forms the foundation by which we improve the performance and effectiveness of our HSEMS. Based on these fundamentals, the HSEMS Manual defines the structural elements vital to the implementation of our HSEMS. These include: the preparation and revision of key HSE documents such as corporate manuals, procedures, and guidelines; the establishment of HSE organizations; HSE technical support for each division; HSE education and training; HSE communication activities; and periodic HSE audits and reviews.
The Nagaoka Field Office, our largest office in Japan, obtained ISO 14001 certification in FY2003 and has maintained this international certification for environmental management systems ever since, in conjunction with our HSEMS.
1 OMS510: IOGP Report No. 510: “Operating Management System Framework for controlling risk and delivering high performance in the oil and gas industry”
HSEMS Structural Diagram
HSE Governance
HSE Management Structure
The Board of Directors and the Executive Committee oversee HSE. Our Corporate HSE Committee comprises the Senior Vice Presidents of our operational organizations that implement and manage operator projects, and head office divisions that manage non-operator projects and subsidiaries, and the General Managers of corporate divisions. The Committee meets regularly to propose and implement the Group’s initiatives for tackling HSE challenges, analyze risks and opportunities, and monitor the operating status and effectiveness of the HSEMS. Important Group-wide matters resolved by the Committee are then discussed by the Executive Committee and the Board of Directors.
HSE Objectives and Programs
To ensure the continuous improvement of our HSEMS and achieve Group-wide HSE management. We do this by setting annual HSE objectives, developing and executing annual HSE programs to achieve these HSE objectives, and managing improvement progress. The key achievements of our FY2023 HSE programs were as follows:
- We established and conducted a Group-wide “safety month” campaign from September to October. We used the catchphrases “time in field” (prioritizing the workplace) and “speak up” (active dialogue) to enhance occupational safety (thorough compliance with the Life-saving Rules) and process safety management, while encouraging leaders to talk with staff at each site.
- In response to increasing external demands for reduced methane emissions, we had several discussions with relevant internal organizations, leading to the joining of the Oil & Gas Methane Partnership 2.0 (OGMP 2.0). We also enhanced our presence through self-assessment surveys based on the Taskforce on Nature-related Financial Disclosures (TNFD) guidelines, and presentations at workshops with IOGP and national oil companies in Asia, to comply with TNFD, an globally significant body for biodiversity and water, etc.
- As part of preparations for emerging threats, and in consideration of increasing cyber risks, we formulated emergency response plans anticipating attacks on operation and information systems. This was executed in collaboration with the Information Security Committee which also involved leading crisis response drills to strengthen preparedness.
Our FY2024 HSE objectives were created based on The Corporate HSE 4th Phase Mid-Term Strategy (FY 2023 - 2025).
Compliance with HSE Legal Requirements
We engage in our business activities in compliance with the laws of the countries in which we operate our projects.
For our operator projects, we identify legal requirements and manage the compliance status of each project in line with our internal procedure. This assessment outlines the measures for identifying, disseminating, and complying with HSE legal requirements, and responding to their changes. We also regularly update information to reflect new enactments and changes to laws.
For our non-operator projects, we periodically deliberate with related departments regarding the approach to managing and being involved in efforts to comply with HSE legal requirements.
We will continue to coordinate with projects and related departments, both in Japan and overseas, creating systems for managing HSE legal requirements throughout the Group, and complying with all such legal requirements.
HSE Risk Management
To minimize the negative impact of our operator projects, INPEX identifies, analyzes, and assesses HSE risks in accordance with international standards (ISO 31000 and ISO 17776). Before engaging in operations, we confirm risk levels are lowered to acceptable levels.
Furthermore, to achieve the INPEX Vision @2022 goal of “zero major accidents,” we conduct thorough HSE risk management throughout the Group. As part of these efforts, our corporate HSE Unit receives quarterly reports on risks that have potential to lead to major accident events (MAEs2) and the other top 10 risks at all operator projects. We confirm the reported risks are being managed to as low as reasonably practicable (ALARP) level and provide our findings to the Executive Committee.
2 Major accident events (MAEs): Events that cause fatalities, serious injuries, and other serious harm to people and property in the surrounding area, including fires, explosions, and toxic gas clouds resulting from large-scale leakages
Fostering of HSE Culture
To establish a mentality that prioritizes HSE within our organization, we have engaged in ongoing efforts to foster a strong HSE culture. This includes developing our HSEMS, providing HSE education and training, and sharing what we have learned from incidents through the course of our incident investigations (Learning from Incidents: LFI) with all employees.
As an additional effort aimed to foster HSE culture, we present annual Corporate HSE Awards. These awards aim to motivate and raise HSE awareness within organizations, divisions, and individuals, as well as improving Group-wide HSE performance. In FY2023, six awards in total were presented, with the HSE Excellence Award presented to one group and HSE Activity Awards given to three groups and two individuals.
We believe that our senior management must lead the way in our efforts to raise HSE awareness among our employees and the proactively implement HSE activities.
To realize “Safety Number One,” one of the INPEX Values, we also conduct HSE management site visits which enable senior management executives to observe field operations firsthand, helping to gain a better understanding of the risks involved and directly reinforce the significance of HSE to those in operational sites. During FY2023, senior management executives participated in HSE management site visits to a total of 11 sites in Japan and overseas.
Management Site Visits
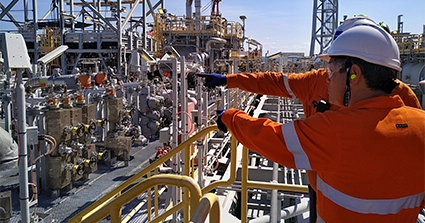
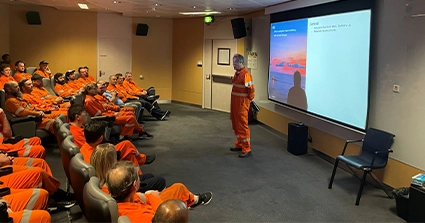
In May, our Director in charge of HSE visited three onshore and offshore sites of the Ichthys LNG Project. During the visit, the Director told employees that while continuous production and operation are needed, the sites require a lot of maintenance work. Therefore, there may need to be a trade-off sometimes between production/operation and safety, which may entail actions such as production stoppages. This emphasized the point of safety first, a policy that must never be compromised.
In August, our President & CEO visited the fifth phase construction site of the New Tokyo Line. His visit reaffirmed that regular visits to the site by our management, as the customers in this case, increases the safety culture at the site that results in an accident-free workplace.
At all sites, senior management executives demonstrate HSE management leadership. The visits were valuable opportunities for senior management and site employees to communicate directly about HSE initiatives and challenges. By engaging senior management to deliver a unified HSE management message to each site, these visits aim to increase overall HSE awareness throughout the Group. We will continue to conduct HSE management site visits in FY2024.
Annually in September, a HSE Forum is held, bringing together operational organization HSE personnel, and representatives of head office operational and corporate divisions for intensive discussions on Group-wide HSE issues.
With the settling of COVID-19, FY2024 saw an increase in global activity. In response, we established and conducted a Group-wide “safety month” campaign from September to October. Using the catchphrases “time in field” (prioritizing the workplace) and “speak up” (active dialogue) to enhance occupational safety (thorough compliance with the Life-saving Rules) and process safety management, we encouraged leaders to talk with staff at each site. We also held internal seminars on the topics of succession and thoughts about safety, learning from incidents, and being aware of subtle danger signals. From video messages from the President & CEO to Group-wide distribution of posters, we implemented a range of measures, resulting in greater safety awareness across the Group.
Annual HSE Meetings

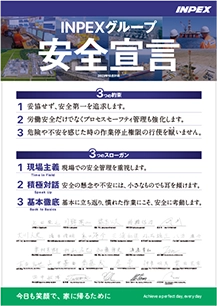
At our Annual HSE Meeting in November, we reflected on the “safety month” campaign and discussed safety activities for the next fiscal year. As our commitment toward safety, attendees at the meeting, including the President & CEO, other senior management executives, and site leaders, all signed the Safety Declaration.
Education and Training for Enhanced HSE Competency
In FY2023, we conducted 2,245.5 person-hours of HSE education and training via internal workshops and training sessions. In addition, for junior technical employees, we provide ongoing hands-on outside training opportunities, both in Japan and overseas, so they can acquire practical occupational safety management and process safety engineering skills.
We also develop job competency profiles by field for our HSE personnel and encourage them to further develop their HSE competencies through on-the-job training (OJT), opportunities and participation in training sessions offered by external organizations specializing in HSE. We will continue to provide training opportunities to employees in FY2024 as we strive to raise the level of their HSE competencies.
HSE Assurance
We periodically conduct HSE audits and reviews to evaluate if the HSEMS is being put to full and steady use in our operator projects and corporate divisions, with the aim of strengthening HSE assurance. To do this, every year we formulate a corporate HSE auditing program and periodically perform HSE audits of operational organizations and the corporate HSE Unit. HSE audits are conducted by internal Lead Auditors with an equivalent level of training to someone with international certification from the International Register of Certificated Auditors (IRCA). In FY2023, we conducted risk-based corporate HSE audits3 for two domestic operational organizations. The results of the HSE audits are reflected in improvements to the HSEMS as necessary.
We also conduct internal reviews to evaluate projects from technical and economic perspectives when considering: new projects led by domestic and overseas operational organizations; non-operator project participation planned by head office divisions; and projects under the five net zero businesses, such as hydrogen and ammonia projects at individual sites. HSE-focused evaluations of projects are also conducted. The results of the evaluations are used to formulate corrective actions, based on mutual agreement. The progress of these corrective actions is then tracked and HSE operation support is provided as necessary, promoting ongoing improvements by steadily implementing corrective actions.
3 Risk-based corporate HSE audits: A methodology for narrowing audit focus to areas with greater risk by considering risks inherent in the organization